For the last 15 years and counting, Engineering News-Record has ranked Turner Construction Company the #1 Green Contractor in the United States. While Turner has countless green building across the globe, they also have 13 LEED certified buildings here in Kendall Square – including 6 Gold, 3 Platinum, and 2 Silver LEED buildings – and that number will only continue to grow. Turner is not just a builder of green buildings, but being a green builder is at the heart of all their work.
As a company, they have diverted more than three million tons of construction waste from landfills, improved on site work environments, and reduced their environmental impact through several programs and initiatives. What makes Turner different is recognizing that these efforts alone are not enough as they continue to seek new and enhanced ways to utilize technical expertise to create a healthy, prosperous, and sustainable future in construction.
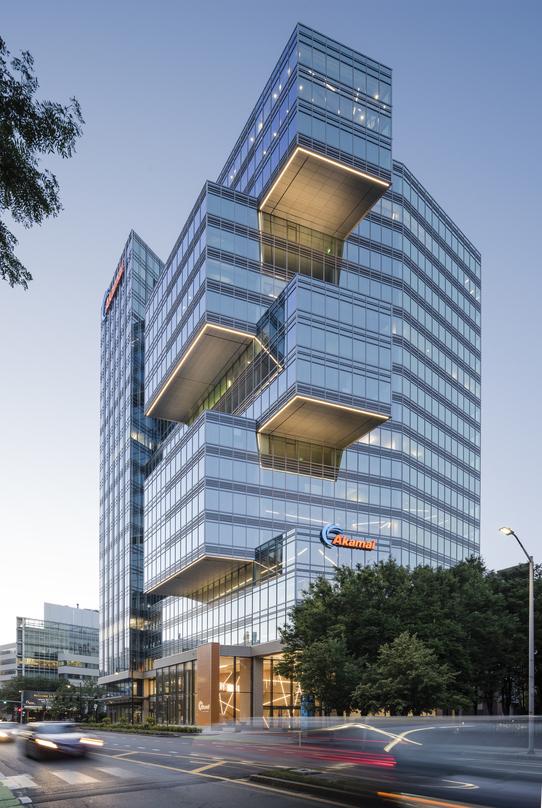
Turner concentrates on addressing internal food waste, building internal sustainability knowledge and capacity, building green construction sites, and contributing to sustainable building life cycles. What’s more, building materials have high embodied carbon. Concrete, for example, makes up 49% of embodied carbon. Due to the amount of carbon found in construction materials, Turner is also focused on addressing embodied carbons, especially in concrete and steel.
The company has engaged in the following sustainability work:
Addressing Food Waste
Turner has a pilot composting program in their Seaport office that, to date, has composted 630 pounds of waste at their main office. In addition, a composting program at one of Turner’s Kendall Square construction projects composted 450 pounds of food waste – diverting almost half a ton of waste from landfills.
Creating Internal Sustainability Working Groups
The company created monthly meetings with subject matter experts in embodied carbon, jobsite carbon and water usage, energy, resilient building design, circular economy, and building accreditation to share knowledge nationally and inform the operations of local business offices. The council of subject matter experts are focused on growing Turner’s knowledge base to ensure continued growth as the top green builder in the nation.
Ensuring Greener Construction Sites
On Turner’s construction sites, the company instituted a no idling policy where all vehicles within the jobsite fence (including, but not limited to, transportation and construction equipment, delivery trucks, and personal or company trucks) shall not idle. This policy contributes to the company’s quadruple bottom line of caring for its employees, the planet, gaining extra LEED certification points, and saving fuel. Eliminating idling from the jobsites aligns with the commitments to Active Caring, Lean Culture, and Sustaining Life. This provides a safer jobsite, happier neighbors, and cost savings without any upcharge.
The company is using LED lamps in all temporary construction lighting in lieu of incandescent, halogen, or fluorescent lights. This nominal initial investment reduces labor and utility costs, has no hazardous waste and provides better quality light for more productivity and increased safety.
Building a More Sustainable Lifecycle
Turner’s focus of making its building life cycles more sustainable is evidenced by their waste management practices. For example, in a project they did with the City of Boston, they demolished several small buildings, and partnered with developers in Tanzania to send seven shipping containers of good quality building materials taken from the demolition to the country, where it was used to build an university.
The company partnered with the nonprofit, The Furniture Trust, in the past to provide gently used office furnishings to local businesses, thereby providing an economical and environmentally responsible solution for otherwise unused office furniture.
Reducing Embodied Carbon
Turner is heavily focused on reducing their embodied carbon and are helping their clients do the same. They have several buildings that will reduce embodied carbon in concrete, and are able to reduce embodied carbon in concrete with little or no upcharge. Turner released an Embodied Carbon Baseline Report in 2022 reflecting emerging trends in the greenhouse gas emissions associated with a sample of their projects’ material footprint. The report corroborates widely accepted conclusions relating to the embodied carbon footprint of commercial buildings in the United States.
In addition, the company has two working committees focused on reducing embodied carbon. The first group focuses on programmatic integrations of embodied carbon considerations into our business model, and includes full-time sustainability managers and design specialists from the Turner Engineering Group (TEG), as well as heads from the estimating, purchasing, technical services, and Virtual Design and Construction (VDC) departments. The second group focuses entirely on concrete embodied carbon reduction, and includes managers and design specialists from our self-perform concrete operations, estimating, sustainability, and structural engineering departments. To date, this group has interviewed and researched over 14 emerging concrete technologies and rolled out company-wide educational material on the use of concrete sensors as a reduction approach.